TIPOS DE HORNOS
Entendemos por hornos industriales los equipos o dispositivos utilizados en la industria, en los que se calientan las piezas o elementos colocados en su interior por encima de la temperatura ambiente. El objeto de este calentamiento puede ser muy variado, por ejemplo:
- Fundir.
- Ablandar para una operación de conformación posterior.
- Tratar térmica mente para impartir determinadas propiedades
- Recubrir las piezas con otros elementos, operación que se facilita frecuentemente operando a temperatura superior a la del ambiente.
- Para evitar ambigüedades en este estudio denominaremos hornos a todos aquellos equipos o instalaciones que operan, en todo o en parte del proceso, a temperatura superior a la ambiente, realizándose el calentamiento de forma directa sobre las piezas (inducción, perdidas dieléctricas, resistencia propia) o de forma indirecta por transmisión de calor de otros elementos (resistencias eléctricas, tubos radiantes eléctricos o de combustión, hornos de llamas, etc.). Esta transmisión de calor puede realizarse por llamas (lecho fluidificado), convección (hornos con fuerte recirculación de los humos, del aire o de la atmósfera protectora sobre las piezas) y radiación (de resistencias, de tubos radiantes, de llamas o de las paredes refractarias interiores).Unicamente consideramos los hornos industriales, es decir, los utilizados en todo tipo de industria, dejando fuera los hornos domésticos, por ejemplo.La energía calorífica requerida para el calentamiento de los hornos puede proceder de:
- Gases calientes producidos en la combustión de combustibles sólidos, líquidos o gaseosos que calientan las piezas por contacto directo entre ambos o indirectamente a través de tubos radiantes o intercambiadores en general.
- Energía eléctrica en diversas formas:
- Arco voltaico de corriente alterna o continua
- Inducción electromagnética
- Alta frecuencia en forma de dielectricidad o microondas
- Resistencia óhmica directa de las piezas
- Resistencias eléctricas dispuestas en el horno que se calientan por efecto Joule y ceden calor a la carga por las diversas formas de transmisión de calor. A los hornos industriales que se calientan por este medio se denominan hornos de resistencias.
- A continuacion los diferentes tipos de hornos:
- Alto Horno

Un alto horno típico está formado por una cápsula cilíndrica de acero de unos 30 metros de alto forrada con un material no metálico y resistente al calor, como asbesto o ladrillos refractarios. El diámetro de la cápsula disminuye hacia arriba y hacia abajo, y es máximo en un punto situado aproximadamente a una cuarta parte de su altura total.
La parte inferior del horno está dotada de varias aberturas tubulares llamadas toberas, por donde se fuerza el paso del aire que enciende el coque.
Cerca del fondo se encuentra un orificio por el que fluye el arrabio cuando se sangra (o vacía) el alto horno. Encima de ese orificio, pero debajo de las toberas, hay otro agujero para retirar la escoria.
La parte superior del horno contiene respiraderos para los gases de escape, y un par de tolvas redondas, cerradas por válvulas en forma de campana, por las que se introduce el mineral de hierro, el coque y la caliza.
Una vez obtenido el arrabio líquido, se puede introducir en distintos tipos de coladura para obtener unos materiales determinados: la colada convencional, de la que se obtienen productos acabados; la colada continua, de la que se obtienen trenes de laminación y, finalmente, la colada sobre lingoteras, de la que lógicamente se obtienen lingotes.
Mejoras en la duración del alto horno
Crisol de material refractario a base de carbono con muy alta conductividad térmica (el enfriamiento del crisol crea una capa de fundición solidificada que protege los ladrillos). La vida del crisol se ha duplicado en 30 años: era de 10 años en 1980, la duración actual es de 20 años. Este factor es esencial, dado que la reparación de un alto horno viene dictada por el estado de su crisol y que esta reparación puede costar, en 2010, unos 100 millones de euros.
Mejora del enfriamiento de la cuba. El objetivo es crear una capa protectora que proteja las paredes de la abrasión producida por el mineral.
Mejoras ambientales
Construcción en circuito cerrado de los circuitos de agua de refrigeración y granulación de la escoria.1
Recuperación del calor, sobre todo de los gases de los hornos de recalentamiento de aire (estufas).1
La recuperación de energía de los gases captados en las entradas de aire por un generador de turbina.1
La condensación de los vapores, especialmente los producidos durante la granulación de la escoria para evitar la emisión de dióxido de azufre o ácido sulfhídrico.1
El reciclaje del carbono para evitar la emisión de gases de efecto invernadero. El objetivo de la investigación actual es la inyección en las toberas de los gases capturados en la boca del horno, en lugar de quemarlos para producir electricidad2
Mejoras en la duración del alto horno
Crisol de material refractario a base de carbono con muy alta conductividad térmica (el enfriamiento del crisol crea una capa de fundición solidificada que protege los ladrillos). La vida del crisol se ha duplicado en 30 años: era de 10 años en 1980, la duración actual es de 20 años. Este factor es esencial, dado que la reparación de un alto horno viene dictada por el estado de su crisol y que esta reparación puede costar, en 2010, unos 100 millones de euros.
Mejora del enfriamiento de la cuba. El objetivo es crear una capa protectora que proteja las paredes de la abrasión producida por el mineral.
Mejoras ambientales
Construcción en circuito cerrado de los circuitos de agua de refrigeración y granulación de la escoria.1
Recuperación del calor, sobre todo de los gases de los hornos de recalentamiento de aire (estufas).1
La recuperación de energía de los gases captados en las entradas de aire por un generador de turbina.1
La condensación de los vapores, especialmente los producidos durante la granulación de la escoria para evitar la emisión de dióxido de azufre o ácido sulfhídrico.1
El reciclaje del carbono para evitar la emisión de gases de efecto invernadero. El objetivo de la investigación actual es la inyección en las toberas de los gases capturados en la boca del horno, en lugar de quemarlos para producir electricidad.
https://www.youtube.com/watch?v=-tYQ_qd4Lt4
HORNO DE BESSEMER
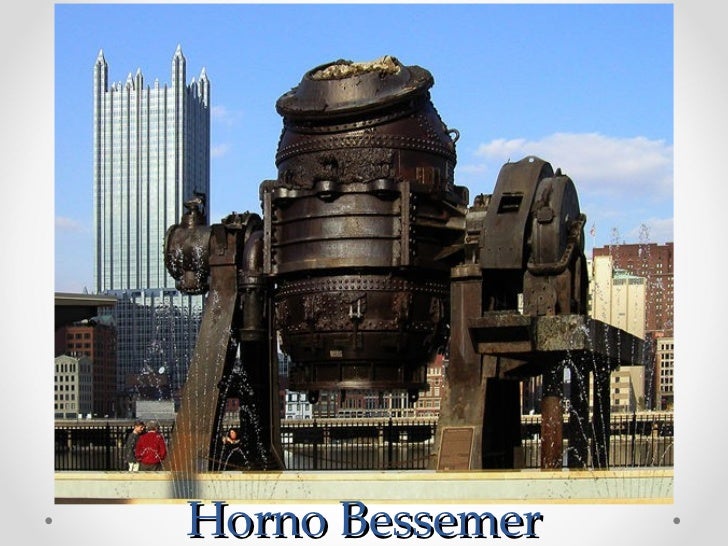
El procedimiento Bessemer fue el primer proceso de fabricación químico que sirvió para la fabricación en serie de acero, fundido en lingotes, de buena calidad y con poco coste a partir del arrabio. Este procedimiento fue llamado así en honor de Henry Bessemer, quien obtuvo la patente en 1855 y la utilizó a través de la Henry Bessemer and Company, sociedad implantada en Sheffield, ciudad del Norte de Inglaterra.
El procedimiento fue descubierto de forma independiente en 1851 por William Kelly.1 2 El mismo también había sido usado fuera de Europa durante cientos de años, pero no a una escala industrial.3 El principio clave es la retirada de impurezas del hierro mediante la oxidación producida por el insuflado de aire en el hierro fundido. La oxidación causa la elevación de la temperatura de la masa de hierro y lo mantiene fundido.
https://www.youtube.com/watch?v=dypdoLm4Rn8
HORNO BASICO DE OXIGENO
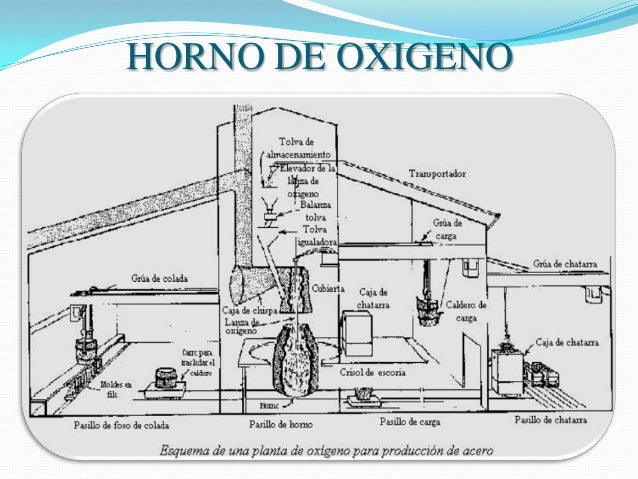
Horno Básico de Oxigeno (BOF)
El nombre del horno se debe a que tiene un recubrimiento de refractario de la línea básica y a la inyección del oxígeno.
Este horno fue inventado por Sir Henrry Bessemer a mediados de 1800
El Proceso BOF se origino en Austria en 1952, fue hecho para convertir arrabio con bajo contenido de fosforo (0.3%) se bautizo con las iniciales LD Lanza de Linz, Luego la técnica se extendió para arrabios de alto fosforo, mediante la adición al chorro de oxigeno de polvo de piedra caliza. Entonces se logro la producción de aceros con arrabio de contenidos con alto fosforo que llegan al 2%.
PARTES
• Cámara de Acero, recubierta por dentro con material refractario, montada en chumaceras que le permiten girar
• Lanza de oxigeno enfriada con agua
¿QUE SE LE AGREGA?
• 75% de Arrabio (Metal Caliente)
• Chatarra (que se encuentra en cajas previamente pesada)
• *Carbono
• *Ferroaleaciones
• A través de la lanza se le inyecta oxigeno y polvo de piedra caliza
PROCESO:
1. Se inclina el horno Con ayuda de una grúa puente y se añade el arrabio, el fundente y a veces chatarra
2. Se pone el horno en vertical y se baja la lanza para inyectar oxigeno (se lleva aproximadamente un tiempo de 15 minutos). En el metal fundido las impurezas se queman; el oxigeno reacciona con el carbono del arrabio y lo elimina en forma de bióxido/ monóxido de carbono.
3. Se inclina el horno y se saca la escoria que flota sobre el acero
4. Se vierte el acero sobre la cuchara y se añaden carbono y ferroaleaciones
QUE RESULTA
• Acero fundido
• Refinación del arrabio
NOTA
• La carga y descarga de la olla se hace por la parte superior
• La temperatura de operación del horno es superior a los 1650°C y
• Es considerado como el sistema más eficiente para la producción de acero de alta calidad.
• La carga metálica para realizar una colada de acero en un convertidor al oxígeno (en un tiempo que varía de 45 a 55 minutos) consiste en arrabio y chatarra; adicionalmente se cargan fundentes como cal siderúrgica y cal dolomítica para formar una escoria para refinación.
• Una acería BOF está dividida en secciones bien definidas de acuerdo con las operaciones que se desarrollan en cada una de ellas: nave de convertidores, nave de carga, nave de colada e instalaciones auxiliares.
• La razón de la inyección de oxígeno es que éste actuará como agente oxidante, ya que al entrar en contacto con la carga se combina químicamente con los elementos de la misma, eliminando en gran parte el contenido de impurezas tales como carbón, fósforo, azufre, silicio, etc.
* El gas monóxido formado es reunido por una chimenea que se encuentra sobre la boca del convertidor y conducido a un depurador de gases, donde es llevado, ya limpio, a la atmósfera.
* El acero procesado en el convertidor se vacía en una olla en la que se le adicionan las ferro-aleaciones necesarias según el tipo de acero a obtener.
* El convertidor se inclina solo hasta vaciar todo el acero, y en otra olla se vacía la escoria que se formó durante el proceso.
https://www.youtube.com/watch?v=coexBFa6OUw
HORNO DE HOGAR ABIERTO

HORNO ARCO ELECTRICO
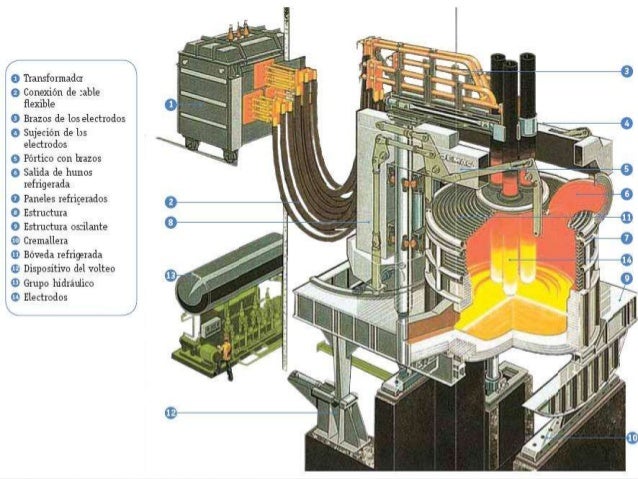
Los hornos de fusión más comunes son los de tipo de arco eléctrico. En este tipo de hornos, el arco pasa entre los electrodos a través de la chatarra. La corriente se suministra a los electrodos por medio de un transformador que regula el voltaje y los parámetros de la corriente de cada estadio de fusión.
El diseño de un horno se estudia para:
Coladas libres de escoria.
Una larga vida de los electrodos.
Una buena homogeneización del acero líquido.
Facilitar el cambio de refractarios.
Funcionar fácilmente por medio de un sistema integrado de combustión, post combustión, inyección de oxígeno e inyección de carbono.
Tomar decisiones de acuerdo con la mejor utilización de energía.
Reducir pérdidas de calor por medio de un diseño adecuado de paneles.
Funcionar con arcos largos y estables y con baja intensidad de corriente de electrodos.
https://www.youtube.com/watch?v=0bKbBJUR7hk
HORNO DE REFINACION

Horno cuchara se utiliza para el afinado del acero horno de fusión temprana ( Horno de arco eléctrico , horno de inducción , convertidor horno , etc ), Y es capaz de regular la temperatura del acero, artesanía tampón Proceso y otras funciones , Conocida como la mejor línea de producción (a principios de horno + LF + colada continua ) alma.Refinado acero para rodamientos , acero de aleación , acero para herramientas , acero para muelles, acero estructural de carbono.
Característica:
Composición del acero líquido, uniformidad de la temperature.
desulfuración , desgasificación, desoxigena,vaya a las inclusiones no metálicas.
mejorar la productividad de los equipos
La adopción de nuevas tecnologías:
Agua Tubular - cover paquete refrigerado
Los dispositivos de elevación de los electrodos ( de un solo brazo , de tres brazos )
Optimizar la estructura de la red de corto (ahorro de energía)
Control PLC electrodo regulador elevación automática
Control automático de argón sistema de soplado
El control de frecuencia auto cucharón
Automatización y control industrial
La tecnología de red
Funciones principales
1. El horno de refinación de cuchara puede regular la temperatura del acero fundido apropiadamente. Por medio de una calefacción de arco eléctrico, el acero fundido obtiene nueva energía térmica. Esto no sólo puede añadir y ajustar la composición de la aleación, sino también reponer la escoria, con lo facilita la desulfuración profunda y de la desoxidación del acero fundido. La temperatura de vertido abierto del acero fundido requerida para la colada continua está garantizada, mejorando además la calidad de la losa.
2. Puede batir el acero fundido con el gas argón que entra en el acero fundido a través del ladrillo de aire instalado en la parte inferior de la cuchara.
3 Esta serie de horno de cuchara, para refinación también posee la función de desgasificación al vacío. Después de ser suspendido en el interior del recipiente de vacío, la cuchara se desgasifica con la bomba de vacío por chorro de vapor y mientras tanto el gas argón es soplado desde la parte inferior de la cuchara de colada, para agitar el acero fundido. De esta manera, el hidrógeno y el nitrógeno puede ser retirado y al mismo tiempo, el oxígeno y el contenido de azufre se reducen aún más, con lo que en última instancia lograr un acero de alta pureza líquido y materiales de rendimiento superior.
Nuestra empresa es un fabricante especializado de hornos de cuchara para refinación con sede en China. Ofrecemos una amplia gama de productos, incluyendo: hornos de sinterización de carbono al vacío, hornos eléctricos, hornos de inducción de media frecuencia y más.
https://www.youtube.com/watch?v=_KwE7h-OVCk
HORNO DE INDUCCION
Z
Los hornos de inducción se utilizan en una amplia gama de instalaciones para producción y fabricación, tales como fundiciones y plantas metalúrgicas. Los hornos de inducción se utilizan sobre todo porque son bastante limpios, pueden derretir materiales con rapidez, y en general son asequibles para mantener y operar. También permiten un control preciso de la temperatura y el calor. Debido a que ganan calor muy rápidamente no se deben dejar en marcha entre operaciones para así ahorrar en recursos energéticos y ayudar a administrar los costos de operación.
El principio de calentamiento de un metal por medio de la inducción fue descubierto por Michael Faraday en 1831 mientras se encontraba experimentando en su laboratorio.1
Una ventaja del horno de inducción es que es limpio, eficiente desde el punto de vista energético, y es un proceso de fundición y de tratamiento de metales más controlable que con la mayoría de los demás modos de calentamiento. Otra de sus ventajas es la capacidad para generar una gran cantidad de calor de manera rápida. Los principales componentes de un sistema de calentamiento por inducción son: el cuerpo de bobinas , conformado por las bobinas de fuerza (donde como están dispuestas físicamente es donde hay mayor agitación del baño líquido) y por las bobinas de refrigeración , la fuente de alimentación, la etapa de acoplamiento de la carga, una estación de enfriamiento, el material refractario que protege a las bobinas del baño líquido y la pieza a ser tratada.1
Las fundiciones más modernas utilizan este tipo de horno y cada vez más fundiciones están sustituyendo los altos hornos por los de inducción, debido a que aquellos generaban mucho polvo entre otros contaminantes. El rango de capacidades de los hornos de inducción abarca desde menos de un kilogramo hasta cien toneladas y son utilizados para fundir hierro y acero, cobre, aluminio y metales preciosos. Uno de los principales inconvenientes de estos hornos es la imposibilidad de refinamiento; la carga de materiales ha de estar libre de productos oxidantes y ser de una composición conocida y algunas aleaciones pueden perderse debido a la oxidación (y deben ser re-añadidos).
El rango de frecuencias de operación va desde la frecuencia de red (50 ó 60 Hz) hasta los 10 kHz, en función del metal que se quiere fundir, la capacidad del horno y la velocidad de fundición deseada - normalmente un horno de frecuencia elevada (más de 3000 Hz) es más rápido, siendo utilizados generalmente en la fundición de aceros, dado que la elevada frecuencia disminuye la turbulencia y evita la oxidación. Frecuencias menores generan más turbulencias en el metal, reduciendo la potencia que puede aplicarse al metal fundido.
En la actualidad los hornos de frecuencia de línea (50 ó 60 Hz, según país) han quedado en desuso, ya que los mismos poseían muy poca eficiencia energética y además cargaban con un alto coste de mantenimiento, dado que contenían una gran cantidad de elementos electromecánicos. En las últimas décadas (aproximadamente desde finales de la década de 1970) se han incorporado equipos de estado sólido, conformados en su etapa de potencia con componentes tales como tiristores (diodos SCR) y transistores de potencia tipo IGBT, con lo que el rendimiento y eficiencia de estos equipos ha aumentado considerablemente.
Un horno para una tonelada precalentado puede fundir una carga fría en menos de una hora. En la práctica se considera que se necesitan 600 kW para fundir una tonelada de hierro en una hora.
Un horno de inducción en funcionamiento normalmente emite un zumbido, silbido o chirrido (debido a la magnetostricción), cuya frecuencia puede ser utilizada por los operarios con experiencia para saber si el horno funciona correctamente o a qué potencia lo está haciendo.
https://www.youtube.com/watch?v=_KwE7h-OVCk
HORNO DE CRISOL

Uno de los usos más primitivos del crisol fue la elaboración y obtención del platino para hacer metales acrisolados. Más recientemente, los metales tales como el níquel y el circonio se han empleado en el crisol. Los metales acrisolados se elaboran, o se trabajan a grandes temperaturas para ser incluidos en una especie de molde. Los moldes permiten que los gases se expandan y se liberen durante su enfriamiento. Los moldes se pueden fabricar de muchas formas y de varios tamaños, pero rara vez de tamaños de menos de 10–15 milímetros; en estos casos suelen ser de porcelana.
Un crisol es igualmente un contenedor en el que un metal se funde, por regla general a temperaturas por encima de los 500 °C. Estos crisoles se elaboran a menudo de grafito con barro como ligazón entre los materiales. Estos crisoles son muy durables y resistentes a temperaturas por encima de los 1600 °C. Un crisol suele colocarse de forma habitual en un horno y cuando el metal se ha fundido se vierte en un molde. Algunos hornos (generalmente los de inducción o eléctricos) tienen embebidos los crisoles.
Este tipo es el más sencillo de los hornos y todavía se encuentran en algunas pequeñas fundiciones que trabajan aleaciones de metales no férreos. En las fundiciones que trabajan con hierro fundido pueden tener emplea para coladas pequeñas y urgentes. No se emplea para el acero, a pesar de que es un hecho cierto que los mejores aceros ingleses del siglo pasada eran obtenidas en baterías de este tipo de hornos. Están constituidas de un crisol de grafito apoyado sobre ladrillos refractarios y rodeados por todas partes de coque partido que se enciende, alcanza la incandescencia por la inyección de aire. El crisol alcanza de este modo temperaturas mas elevadas y la carga metálica que contiene se funde sin entrar en contacto con los gases de combustión.
El elemento mas importante es el crisol, compuesto de grafito con la adición eventual de un carburante, mezclado con aglutinantes adecuados, por ejemplo arcilla o alquitrán. Los crisoles se construyen con estampas de acero sobre la que es fuertemente prensado el material de aquellos. Se acaban en el torno, y después de secados se introducen en cajones de material refractario y se someten a acción en hornos adecuados a temperaturas elevadas.
Horno de crisol inclinable, con precalentamiento de aire
Los hornos de crisol fijo tienen el gran inconveniente de que el metal debe ser extraído en pequeñas cantidades, con cucharas a menos de que la colada se efectuara directamente en alguna forma. Para evitar este inconveniente y para utilizar el calor sensible de los gases de combustión, se construyeron los hornos de crisoles inclinables, mecánica o hidráulicamente, y que pueden tener un sistema de precalentamiento de aire.
https://www.youtube.com/watch?v=l7E4gD7mukI
HORNO DE CUBILOTE

A pesar de que la primera patente de lo que se considera el cubilote moderno cumplió en 1994 doscientos años de ser otorgada a John Wilkinson (Inglaterra), se puede decir que el cubilote mantiene su diseño fundamental hasta nuestros días. Naturalmente, ha sufrido variaciones estructurales, se le han incorporado aditamentos, se han rediseñado algunas de sus partes, particularmente el sistema de toberas, pero su concepción inicial de horno tubular, en posición vertical, con la entrada de la carga metálica por la parte superior y un contacto directo entre el combustible sólido y dicha carga metálica, se ha mantenido inalterable.
Esto se debe a una causa fundamental: el cubilote posee una eficiencia de fusión alta en comparación con los demás hornos empleados con el mismo fin. Esto se explica, porque en este tipo de horno la carga metálica a fundir (arrabio, chatarra de acero, ferroaleaciones, rechazos de la producción, etc.), está en contacto directo con el combustible sólido (coque), que se emplea para su fusión. Esta eficiencia de fusión se entiende como la relación que existe entre el calor potencial que hay en el hierro fundido que sale del cubilote y el total del calor que entra al proceso (combustión de coque, procesos de oxidación de índole exotérmica y calor sensible en el aire que se sopla dentro del horno). Así, por ejemplo, en condiciones favorables de eficiencia (empleando soplo caliente), se pueden alcanzar valores algo superiores al 40 %. En cambio, en condiciones muy desfavorables (soplo frío, revestimiento del horno en mal estado, mala operación del horno, etc.), este valor puede descender hasta 30 % o más. Sin embargo, la eficiencia de la combustión en este tipo de horno no sobrepasa el 60 al 70 %, lo cual es un valor bajo en comparación con los demás hornos que queman combustible. Esto se debe, principalmente, a que no se puede hacer un uso total del contenido calórico del coque sin interferir en los requerimientos metalúrgicos del proceso, en tanto, el coque y sus gases de combustión son elementos activos en dicho proceso.
Por todo lo expresado hasta aquí, es que se ha afirmado que operar bien un cubilote no es tanto controlar un proceso metalúrgico, como dirigir una combustión. Por ese motivo, todo lo concerniente a las características del combustible empleado, así como el volumen y presión del aire que se introduce en el horno (sin olvidar la humedad relativa), posee una importancia primordial para la buena marcha del mismo. Paralelo a esto, el horno debe poseer determinadas relaciones entre sus parámetros de diseño, de manera tal que el proceso de combustión que se produzca dentro de él permita obtener un hierro fundido a la temperatura requerida.
El presente trabajo tiene como objetivo relacionar los parámetros de diseño y operación, mediante una metodología pre-establecida, de manera que se obtenga un cuadro general que caracterice el horno objeto de análisis.
Introducción.
Estructura.
Estructura y funcionamiento del horno de cubilote.
El cubilote está constituido por las siguientes partes (ver figura No.1, Pág. 7):
Envoltura cilíndrica de chapa de acero soldada.
Revestimiento interno de material refractario (entre este y la envoltura se deja una capa intermedia de unos 2 cm, rellena de arena seca, para permitir las dilataciones radiales y axiales de refractario).
Chimenea y su correspondiente cobertura. Algunas veces se añade apagachispas.
Boca de carga: pequeña y provista de una plancha inclinada para la introducción de las cargas cuando se realizan a mano, más amplia si se hace mecánicamente.
Cámara de aire anular, de plancha delgada, que circunda del todo o en parte la envoltura y dentro de la cual, pasa aire o viento (enviado por una máquina soplante) para la combustión del coque.
Toberas, de hierro colado o chapas de acero, en forma de caja horadada y adaptada al revestimiento para conducir el aire al interior del cubilote. En la parte correspondiente de cada tobera, la pared exterior está agujereada y provista de portillos con mirillas (de mica o cristal) para vigilar la combustión.
Piquera de escoria. Abertura dispuesta a unos 15 o 20 cm aproximadamente por debajo del plano de toberas, inclinada de 30 a 40º, respecto a la horizontal, para facilitar la salida de la escoria.
Puerta lateral de encendido y limpieza. Antes de cerrarla, al comienzo de la fusión, hay que rehacer el murete que completa el revestimiento.
Canal de colada, de plancha de hierro, revestido de masa refractaria. Mantiene la misma inclinación de la solera (10º), para hacer caer el hierro fundido en el caldero de colada.
Solera a fondo de cubilote. Consiste en arena de moldeo apisonada e inclinada 10º hacia la piquera de sangría del horno.
Plancha base de envoltura cilíndrica; de hierro colado o chapa fuerte. En su centro hay una abertura del diámetro de la solera, que puede cerrarse con un portillo de descarga de uno o dos batientes que se abren hacia abajo por medio de un cerrojo, de una palanca o quitando el puntal. A través de ella se descarga el contenido de coque de la cama, al final de la operación del horno.
Columnas de apoyo: casi siempre son cuatro, de hierro fundido y son sostenidas a su vez por unos cimientos de ladrillos de hormigón.
Crisol: es la parte inferior del cubilote comprendido entre la solera y el plano de las toberas. Se estima que el metal ocupa en él, el 46 % del volumen. El 54 % restante está ocupado por coque incandescente.
Funcionamiento del cubilote.
La reparación puede efectuarse también por medio de unos aparatos especialmente creados para este uso, que proyectan la masa refractaria contra las paredes que hay que reparar por medio de aire comprimido. Este sistema es aplicable a los hornos de dimensiones grande y mediana.
Al día siguiente se puede encender de nuevo. Algunas veces se repara durante la noche o la madrugada para fundir todos los días. Aunque esto requiere de un esfuerzo considerable por parte de los reberberistas.
Reparación. – Después de cada fusión de 3 a 10 horas, el cubilote se deja enfriar y, al día siguiente, se repara. A este fin, con un cincel o una piqueta, se quita la escoria o el material refractario vitrificado adherido al revestimiento, que se presenta más o menos corroído en torno a las toberas hasta alcanzar el material refractario que no ha sufrido deterioro. Las partes afectadas se recubren entonces con material nuevo, a mano y dejándolo reposar por lo menos 24 horas. Si el espesor a recubrir es muy grande, se utilizan trozos de ladrillos, siempre del mismo material refractario.
Dos horas antes de dar comienzo a la colada, por la portilla de encendido (o desde arriba) se introduce un montoncito de leña seca que se enciende hasta obtener un fuego abundante y vivo, favorecido por el enérgico tiro que producen la portilla de encendido, las mirillas de las toberas, la piquera de colada y la de escoria, todas abiertas, así como la propia chimenea del horno.
Se empieza entonces a introducir el coque encendido, en una capa de unos 32 cm para cada carga, a razón de 140 Kg por metro cuadrado de horno; con el coque debe mezclarse un 5 a 10 % de piedra caliza, llamada también fundente; antes de introducir una nueva capa hay que asegurarse de que el coque situado debajo esté bien encendido.
El coque de encendido debe alcanzar de 1 a 1.60 metros sobre el plano de toberas. El nivel se comprueba introduciendo por la boca de carga una cadena o una cabilla doblada en (Z), el encendido de la columna se comprueba observando el color rojo del revestimiento refractario u observando directamente los trozos de coque por la mirilla de las toberas. Se activa el encendido dando viento por espacio de 4 a 5 minutos, lo cual sirve también para desulfurar el coque.
Encendido. – Se repara la solera del horno con arena de moldear seca con una pequeña adición de grafito, arcilla y agua, secándose con fuego de leña o con una llama de fuel-oil o de gas.
La carga de coque de encendido (cama), cuya función es sostener las cargas colocadas encima y dar, con su combustión, la energía térmica necesaria, debe estar constituida por una cantidad de combustible cuya altura permanezca invariable durante toda la colada.
Para ello, el coque consumido se reintegra de modo regular a través de las cargas sucesivas de coque, que entran por la puerta de carga.
Introducción de la carga. – La carga del horno comienza colocando sobre la capa de coque de encendido una carga de coque adicionada de la necesaria cantidad de fundente y encima de esta la carga metálica. A continuación se coloca una segunda carga de coque con fundente y la segunda carga metálica, y así alternativamente hasta alcanzar la puerta de carga. A continuación, se espera un período de tiempo de 60 a 90 minutos (según el tamaño del horno), para que el coque encendido de la cama precaliente las cargas añadidas al horno. Transcurrido ese tiempo, se cierran las mirillas de las toberas y las portillas, se conecta el ventilador y si todo ha sido bien ejecutado, transcurrido de 6 a 9 minutos, se presentará el primer hierro fundido en la piquera de colada. Este hierro se considera frío y no se utiliza. Solo se emplea cuando comienza a salir caliente y con buena fluidez por el canal.
En el sistema por sifón (Pinar del Río), desde un inicio el orificio de sangría permanece abierto, el hierro y la escoria se separan en el sifón. Esto es lo que se conoce como colada continua.
Período de operación. – A partir de que el primer hierro fluye libremente por el canal de sangría, se cierra este orificio con un tapón de barro refractario. Se deben disponer de varios tapones (humedecidos, próximos al horno), ya que se utilizarán cada vez que se pique el horno. Ahora se espera a que se acumule el hierro líquido en el crisol del horno. La medida de que el crisol estará lleno le dará la salida de escoria por la piquera correspondiente. La fluidez con que salga la escoria es índice del buen funcionamiento del horno. Inmediatamente que salga toda la escoria (comienza a salir hierro, junto con la escoria), quiere decir que el crisol está lleno de hierro líquido. Entonces se rompe el tapón del orificio de sangría y se recibe el hierro en las cazuelas de vertido. Vaciado el crisol se coloca un nuevo tapón en el orificio de sangría y se repite todo el proceso. Lo descrito aquí es lo que se denomina operar el horno por picada y se hace cuando se demandan grandes cantidades de hierro de una vez o por práctica establecida.
Fin de la fusión. – Después de algunas horas de funcionamiento se comprueba la cantidad de piezas que quedan todavía por colar y se introduce la última carga, reservado para esta los trozos de metal más ligeros. Cuando el nivel de la carga alcanza aproximadamente las tres cuartas partes de la altura del horno, se reduce gradualmente el viento, cerrando por completo la entrada de aire al horno cuando está próxima la fusión del último hierro colado. Cuando aparece escoria en la piquera se vacía el horno.
Vaciado del horno. – Hay que asegurarse de que el pavimento debajo del horno esté bien seco; se abren los portillos de las toberas, se abre el canal de colada y la portilla de encendido y se hace correr cerrojo o el puntal que cierra la puerta inferior del horno. La solera del horno cae al igual que los residuos de la capa de coque y de material contenidos, que se apagan con chorros de agua y se retiran para que no se estropee el cubilote. El coque recuperado se aprovecha para las estufas o para el relleno de machos muy voluminosos. El hierro se funde para las piezas corrientes.
https://www.youtube.com/watch?v=CzImVZSUEl8
MUCHAS GRACIAS POR SU ATENCION !!!!!!!
HORNO DE BESSEMER
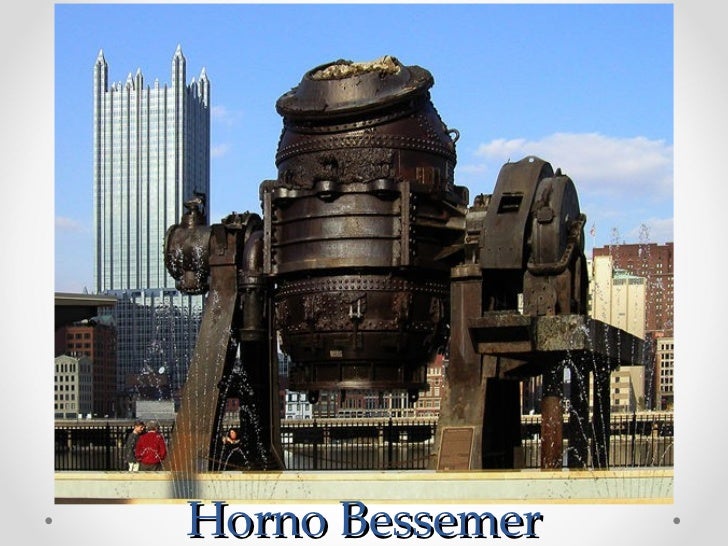
El procedimiento Bessemer fue el primer proceso de fabricación químico que sirvió para la fabricación en serie de acero, fundido en lingotes, de buena calidad y con poco coste a partir del arrabio. Este procedimiento fue llamado así en honor de Henry Bessemer, quien obtuvo la patente en 1855 y la utilizó a través de la Henry Bessemer and Company, sociedad implantada en Sheffield, ciudad del Norte de Inglaterra.
El procedimiento fue descubierto de forma independiente en 1851 por William Kelly.1 2 El mismo también había sido usado fuera de Europa durante cientos de años, pero no a una escala industrial.3 El principio clave es la retirada de impurezas del hierro mediante la oxidación producida por el insuflado de aire en el hierro fundido. La oxidación causa la elevación de la temperatura de la masa de hierro y lo mantiene fundido.
https://www.youtube.com/watch?v=dypdoLm4Rn8
HORNO BASICO DE OXIGENO
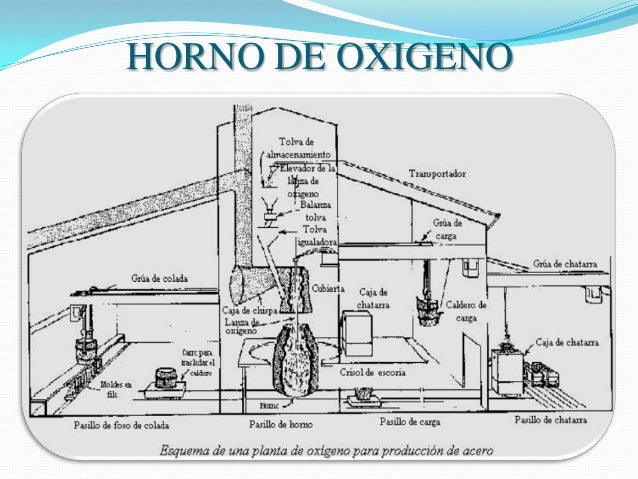
Horno Básico de Oxigeno (BOF)
El nombre del horno se debe a que tiene un recubrimiento de refractario de la línea básica y a la inyección del oxígeno.
Este horno fue inventado por Sir Henrry Bessemer a mediados de 1800
El Proceso BOF se origino en Austria en 1952, fue hecho para convertir arrabio con bajo contenido de fosforo (0.3%) se bautizo con las iniciales LD Lanza de Linz, Luego la técnica se extendió para arrabios de alto fosforo, mediante la adición al chorro de oxigeno de polvo de piedra caliza. Entonces se logro la producción de aceros con arrabio de contenidos con alto fosforo que llegan al 2%.
PARTES
• Cámara de Acero, recubierta por dentro con material refractario, montada en chumaceras que le permiten girar
• Lanza de oxigeno enfriada con agua
¿QUE SE LE AGREGA?
• 75% de Arrabio (Metal Caliente)
• Chatarra (que se encuentra en cajas previamente pesada)
• *Carbono
• *Ferroaleaciones
• A través de la lanza se le inyecta oxigeno y polvo de piedra caliza
PROCESO:
1. Se inclina el horno Con ayuda de una grúa puente y se añade el arrabio, el fundente y a veces chatarra
2. Se pone el horno en vertical y se baja la lanza para inyectar oxigeno (se lleva aproximadamente un tiempo de 15 minutos). En el metal fundido las impurezas se queman; el oxigeno reacciona con el carbono del arrabio y lo elimina en forma de bióxido/ monóxido de carbono.
3. Se inclina el horno y se saca la escoria que flota sobre el acero
4. Se vierte el acero sobre la cuchara y se añaden carbono y ferroaleaciones
QUE RESULTA
• Acero fundido
• Refinación del arrabio
NOTA
• La carga y descarga de la olla se hace por la parte superior
• La temperatura de operación del horno es superior a los 1650°C y
• Es considerado como el sistema más eficiente para la producción de acero de alta calidad.
• La carga metálica para realizar una colada de acero en un convertidor al oxígeno (en un tiempo que varía de 45 a 55 minutos) consiste en arrabio y chatarra; adicionalmente se cargan fundentes como cal siderúrgica y cal dolomítica para formar una escoria para refinación.
• Una acería BOF está dividida en secciones bien definidas de acuerdo con las operaciones que se desarrollan en cada una de ellas: nave de convertidores, nave de carga, nave de colada e instalaciones auxiliares.
• La razón de la inyección de oxígeno es que éste actuará como agente oxidante, ya que al entrar en contacto con la carga se combina químicamente con los elementos de la misma, eliminando en gran parte el contenido de impurezas tales como carbón, fósforo, azufre, silicio, etc.
* El gas monóxido formado es reunido por una chimenea que se encuentra sobre la boca del convertidor y conducido a un depurador de gases, donde es llevado, ya limpio, a la atmósfera.
* El acero procesado en el convertidor se vacía en una olla en la que se le adicionan las ferro-aleaciones necesarias según el tipo de acero a obtener.
* El convertidor se inclina solo hasta vaciar todo el acero, y en otra olla se vacía la escoria que se formó durante el proceso.
https://www.youtube.com/watch?v=coexBFa6OUw
HORNO DE HOGAR ABIERTO
El HORNO DE HOGAR ABIERTO semeja un horno enorme, y se le denomina de esta manera porque contiene en el hogar (fondo) una especie de piscina larga y poco profunda (6m de ancho, por 15 m de largo, por 1 m de profundidad, aproximadamente). |
|
El horno se carga en un 30% a un 40% con chatarra y piedra caliza, empleando aire pre-calentado, combustible líquido y gas para la combustión, largas lenguas de fuego pasan sobre los materiales, fundiéndolos. Al mismo tiempo, se quema (o se oxida) el exceso de carbono y otras impurezas como el fósforo, silicio y manganeso.
Este proceso puede acelerarse introduciendo tubos refrigerados por agua (lanzas), los que suministran un grueso flujo de oxígeno sobre la carga.
Periódicamente, se revisan muestras de la masa fundida en el laboratorio para verificar la composición empleando un instrumento denominado espectrómetro. También se determinan los niveles de carbono.
Si se está fabricando acero de aleación, se agregarán los elementos de aleación deseados. Cuando las lecturas de composición son correctas, el horno se cuela y el acero fundido se vierte en una olla de colada.
El proceso completo demora de cinco a ocho horas, mientras que el Horno de Oxígeno Básico produce la misma cantidad de acero en 45 minutos aproximadamente. Debido a esto, este horno ha sido virtualmente reemplazado por el de Oxígeno Básico.
Este proceso puede acelerarse introduciendo tubos refrigerados por agua (lanzas), los que suministran un grueso flujo de oxígeno sobre la carga.
Periódicamente, se revisan muestras de la masa fundida en el laboratorio para verificar la composición empleando un instrumento denominado espectrómetro. También se determinan los niveles de carbono.
Si se está fabricando acero de aleación, se agregarán los elementos de aleación deseados. Cuando las lecturas de composición son correctas, el horno se cuela y el acero fundido se vierte en una olla de colada.
El proceso completo demora de cinco a ocho horas, mientras que el Horno de Oxígeno Básico produce la misma cantidad de acero en 45 minutos aproximadamente. Debido a esto, este horno ha sido virtualmente reemplazado por el de Oxígeno Básico.
HORNO ARCO ELECTRICO
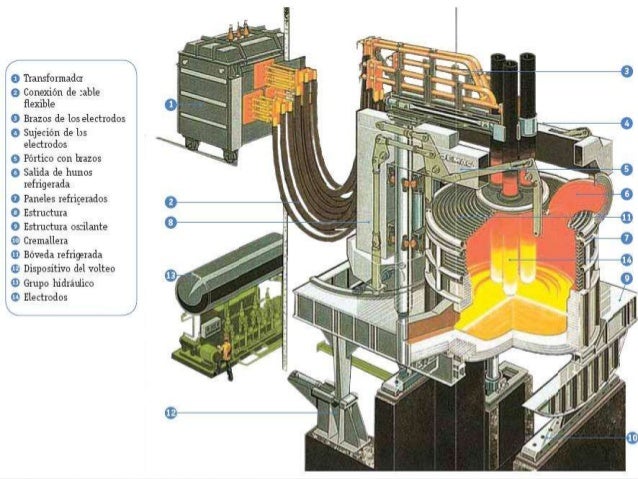
Los hornos de fusión más comunes son los de tipo de arco eléctrico. En este tipo de hornos, el arco pasa entre los electrodos a través de la chatarra. La corriente se suministra a los electrodos por medio de un transformador que regula el voltaje y los parámetros de la corriente de cada estadio de fusión.
El diseño de un horno se estudia para:
Coladas libres de escoria.
Una larga vida de los electrodos.
Una buena homogeneización del acero líquido.
Facilitar el cambio de refractarios.
Funcionar fácilmente por medio de un sistema integrado de combustión, post combustión, inyección de oxígeno e inyección de carbono.
Tomar decisiones de acuerdo con la mejor utilización de energía.
Reducir pérdidas de calor por medio de un diseño adecuado de paneles.
Funcionar con arcos largos y estables y con baja intensidad de corriente de electrodos.
https://www.youtube.com/watch?v=0bKbBJUR7hk
HORNO DE REFINACION

Horno cuchara se utiliza para el afinado del acero horno de fusión temprana ( Horno de arco eléctrico , horno de inducción , convertidor horno , etc ), Y es capaz de regular la temperatura del acero, artesanía tampón Proceso y otras funciones , Conocida como la mejor línea de producción (a principios de horno + LF + colada continua ) alma.Refinado acero para rodamientos , acero de aleación , acero para herramientas , acero para muelles, acero estructural de carbono.
Característica:
Composición del acero líquido, uniformidad de la temperature.
desulfuración , desgasificación, desoxigena,vaya a las inclusiones no metálicas.
mejorar la productividad de los equipos
La adopción de nuevas tecnologías:
Agua Tubular - cover paquete refrigerado
Los dispositivos de elevación de los electrodos ( de un solo brazo , de tres brazos )
Optimizar la estructura de la red de corto (ahorro de energía)
Control PLC electrodo regulador elevación automática
Control automático de argón sistema de soplado
El control de frecuencia auto cucharón
Automatización y control industrial
La tecnología de red
Funciones principales
1. El horno de refinación de cuchara puede regular la temperatura del acero fundido apropiadamente. Por medio de una calefacción de arco eléctrico, el acero fundido obtiene nueva energía térmica. Esto no sólo puede añadir y ajustar la composición de la aleación, sino también reponer la escoria, con lo facilita la desulfuración profunda y de la desoxidación del acero fundido. La temperatura de vertido abierto del acero fundido requerida para la colada continua está garantizada, mejorando además la calidad de la losa.
2. Puede batir el acero fundido con el gas argón que entra en el acero fundido a través del ladrillo de aire instalado en la parte inferior de la cuchara.
3 Esta serie de horno de cuchara, para refinación también posee la función de desgasificación al vacío. Después de ser suspendido en el interior del recipiente de vacío, la cuchara se desgasifica con la bomba de vacío por chorro de vapor y mientras tanto el gas argón es soplado desde la parte inferior de la cuchara de colada, para agitar el acero fundido. De esta manera, el hidrógeno y el nitrógeno puede ser retirado y al mismo tiempo, el oxígeno y el contenido de azufre se reducen aún más, con lo que en última instancia lograr un acero de alta pureza líquido y materiales de rendimiento superior.
Nuestra empresa es un fabricante especializado de hornos de cuchara para refinación con sede en China. Ofrecemos una amplia gama de productos, incluyendo: hornos de sinterización de carbono al vacío, hornos eléctricos, hornos de inducción de media frecuencia y más.
https://www.youtube.com/watch?v=_KwE7h-OVCk
HORNO DE INDUCCION

Los hornos de inducción se utilizan en una amplia gama de instalaciones para producción y fabricación, tales como fundiciones y plantas metalúrgicas. Los hornos de inducción se utilizan sobre todo porque son bastante limpios, pueden derretir materiales con rapidez, y en general son asequibles para mantener y operar. También permiten un control preciso de la temperatura y el calor. Debido a que ganan calor muy rápidamente no se deben dejar en marcha entre operaciones para así ahorrar en recursos energéticos y ayudar a administrar los costos de operación.
El principio de calentamiento de un metal por medio de la inducción fue descubierto por Michael Faraday en 1831 mientras se encontraba experimentando en su laboratorio.1
Una ventaja del horno de inducción es que es limpio, eficiente desde el punto de vista energético, y es un proceso de fundición y de tratamiento de metales más controlable que con la mayoría de los demás modos de calentamiento. Otra de sus ventajas es la capacidad para generar una gran cantidad de calor de manera rápida. Los principales componentes de un sistema de calentamiento por inducción son: el cuerpo de bobinas , conformado por las bobinas de fuerza (donde como están dispuestas físicamente es donde hay mayor agitación del baño líquido) y por las bobinas de refrigeración , la fuente de alimentación, la etapa de acoplamiento de la carga, una estación de enfriamiento, el material refractario que protege a las bobinas del baño líquido y la pieza a ser tratada.1
Las fundiciones más modernas utilizan este tipo de horno y cada vez más fundiciones están sustituyendo los altos hornos por los de inducción, debido a que aquellos generaban mucho polvo entre otros contaminantes. El rango de capacidades de los hornos de inducción abarca desde menos de un kilogramo hasta cien toneladas y son utilizados para fundir hierro y acero, cobre, aluminio y metales preciosos. Uno de los principales inconvenientes de estos hornos es la imposibilidad de refinamiento; la carga de materiales ha de estar libre de productos oxidantes y ser de una composición conocida y algunas aleaciones pueden perderse debido a la oxidación (y deben ser re-añadidos).
El rango de frecuencias de operación va desde la frecuencia de red (50 ó 60 Hz) hasta los 10 kHz, en función del metal que se quiere fundir, la capacidad del horno y la velocidad de fundición deseada - normalmente un horno de frecuencia elevada (más de 3000 Hz) es más rápido, siendo utilizados generalmente en la fundición de aceros, dado que la elevada frecuencia disminuye la turbulencia y evita la oxidación. Frecuencias menores generan más turbulencias en el metal, reduciendo la potencia que puede aplicarse al metal fundido.
En la actualidad los hornos de frecuencia de línea (50 ó 60 Hz, según país) han quedado en desuso, ya que los mismos poseían muy poca eficiencia energética y además cargaban con un alto coste de mantenimiento, dado que contenían una gran cantidad de elementos electromecánicos. En las últimas décadas (aproximadamente desde finales de la década de 1970) se han incorporado equipos de estado sólido, conformados en su etapa de potencia con componentes tales como tiristores (diodos SCR) y transistores de potencia tipo IGBT, con lo que el rendimiento y eficiencia de estos equipos ha aumentado considerablemente.
Un horno para una tonelada precalentado puede fundir una carga fría en menos de una hora. En la práctica se considera que se necesitan 600 kW para fundir una tonelada de hierro en una hora.
Un horno de inducción en funcionamiento normalmente emite un zumbido, silbido o chirrido (debido a la magnetostricción), cuya frecuencia puede ser utilizada por los operarios con experiencia para saber si el horno funciona correctamente o a qué potencia lo está haciendo.
https://www.youtube.com/watch?v=_KwE7h-OVCk
HORNO DE CRISOL

Uno de los usos más primitivos del crisol fue la elaboración y obtención del platino para hacer metales acrisolados. Más recientemente, los metales tales como el níquel y el circonio se han empleado en el crisol. Los metales acrisolados se elaboran, o se trabajan a grandes temperaturas para ser incluidos en una especie de molde. Los moldes permiten que los gases se expandan y se liberen durante su enfriamiento. Los moldes se pueden fabricar de muchas formas y de varios tamaños, pero rara vez de tamaños de menos de 10–15 milímetros; en estos casos suelen ser de porcelana.
Un crisol es igualmente un contenedor en el que un metal se funde, por regla general a temperaturas por encima de los 500 °C. Estos crisoles se elaboran a menudo de grafito con barro como ligazón entre los materiales. Estos crisoles son muy durables y resistentes a temperaturas por encima de los 1600 °C. Un crisol suele colocarse de forma habitual en un horno y cuando el metal se ha fundido se vierte en un molde. Algunos hornos (generalmente los de inducción o eléctricos) tienen embebidos los crisoles.
Este tipo es el más sencillo de los hornos y todavía se encuentran en algunas pequeñas fundiciones que trabajan aleaciones de metales no férreos. En las fundiciones que trabajan con hierro fundido pueden tener emplea para coladas pequeñas y urgentes. No se emplea para el acero, a pesar de que es un hecho cierto que los mejores aceros ingleses del siglo pasada eran obtenidas en baterías de este tipo de hornos. Están constituidas de un crisol de grafito apoyado sobre ladrillos refractarios y rodeados por todas partes de coque partido que se enciende, alcanza la incandescencia por la inyección de aire. El crisol alcanza de este modo temperaturas mas elevadas y la carga metálica que contiene se funde sin entrar en contacto con los gases de combustión.
El elemento mas importante es el crisol, compuesto de grafito con la adición eventual de un carburante, mezclado con aglutinantes adecuados, por ejemplo arcilla o alquitrán. Los crisoles se construyen con estampas de acero sobre la que es fuertemente prensado el material de aquellos. Se acaban en el torno, y después de secados se introducen en cajones de material refractario y se someten a acción en hornos adecuados a temperaturas elevadas.
Horno de crisol inclinable, con precalentamiento de aire
Los hornos de crisol fijo tienen el gran inconveniente de que el metal debe ser extraído en pequeñas cantidades, con cucharas a menos de que la colada se efectuara directamente en alguna forma. Para evitar este inconveniente y para utilizar el calor sensible de los gases de combustión, se construyeron los hornos de crisoles inclinables, mecánica o hidráulicamente, y que pueden tener un sistema de precalentamiento de aire.
https://www.youtube.com/watch?v=l7E4gD7mukI
HORNO DE CUBILOTE
A pesar de que la primera patente de lo que se considera el cubilote moderno cumplió en 1994 doscientos años de ser otorgada a John Wilkinson (Inglaterra), se puede decir que el cubilote mantiene su diseño fundamental hasta nuestros días. Naturalmente, ha sufrido variaciones estructurales, se le han incorporado aditamentos, se han rediseñado algunas de sus partes, particularmente el sistema de toberas, pero su concepción inicial de horno tubular, en posición vertical, con la entrada de la carga metálica por la parte superior y un contacto directo entre el combustible sólido y dicha carga metálica, se ha mantenido inalterable.
Esto se debe a una causa fundamental: el cubilote posee una eficiencia de fusión alta en comparación con los demás hornos empleados con el mismo fin. Esto se explica, porque en este tipo de horno la carga metálica a fundir (arrabio, chatarra de acero, ferroaleaciones, rechazos de la producción, etc.), está en contacto directo con el combustible sólido (coque), que se emplea para su fusión. Esta eficiencia de fusión se entiende como la relación que existe entre el calor potencial que hay en el hierro fundido que sale del cubilote y el total del calor que entra al proceso (combustión de coque, procesos de oxidación de índole exotérmica y calor sensible en el aire que se sopla dentro del horno). Así, por ejemplo, en condiciones favorables de eficiencia (empleando soplo caliente), se pueden alcanzar valores algo superiores al 40 %. En cambio, en condiciones muy desfavorables (soplo frío, revestimiento del horno en mal estado, mala operación del horno, etc.), este valor puede descender hasta 30 % o más. Sin embargo, la eficiencia de la combustión en este tipo de horno no sobrepasa el 60 al 70 %, lo cual es un valor bajo en comparación con los demás hornos que queman combustible. Esto se debe, principalmente, a que no se puede hacer un uso total del contenido calórico del coque sin interferir en los requerimientos metalúrgicos del proceso, en tanto, el coque y sus gases de combustión son elementos activos en dicho proceso.
Por todo lo expresado hasta aquí, es que se ha afirmado que operar bien un cubilote no es tanto controlar un proceso metalúrgico, como dirigir una combustión. Por ese motivo, todo lo concerniente a las características del combustible empleado, así como el volumen y presión del aire que se introduce en el horno (sin olvidar la humedad relativa), posee una importancia primordial para la buena marcha del mismo. Paralelo a esto, el horno debe poseer determinadas relaciones entre sus parámetros de diseño, de manera tal que el proceso de combustión que se produzca dentro de él permita obtener un hierro fundido a la temperatura requerida.
El presente trabajo tiene como objetivo relacionar los parámetros de diseño y operación, mediante una metodología pre-establecida, de manera que se obtenga un cuadro general que caracterice el horno objeto de análisis.
Introducción.
Estructura.
Estructura y funcionamiento del horno de cubilote.
El cubilote está constituido por las siguientes partes (ver figura No.1, Pág. 7):
Envoltura cilíndrica de chapa de acero soldada.
Revestimiento interno de material refractario (entre este y la envoltura se deja una capa intermedia de unos 2 cm, rellena de arena seca, para permitir las dilataciones radiales y axiales de refractario).
Chimenea y su correspondiente cobertura. Algunas veces se añade apagachispas.
Boca de carga: pequeña y provista de una plancha inclinada para la introducción de las cargas cuando se realizan a mano, más amplia si se hace mecánicamente.
Cámara de aire anular, de plancha delgada, que circunda del todo o en parte la envoltura y dentro de la cual, pasa aire o viento (enviado por una máquina soplante) para la combustión del coque.
Toberas, de hierro colado o chapas de acero, en forma de caja horadada y adaptada al revestimiento para conducir el aire al interior del cubilote. En la parte correspondiente de cada tobera, la pared exterior está agujereada y provista de portillos con mirillas (de mica o cristal) para vigilar la combustión.
Piquera de escoria. Abertura dispuesta a unos 15 o 20 cm aproximadamente por debajo del plano de toberas, inclinada de 30 a 40º, respecto a la horizontal, para facilitar la salida de la escoria.
Puerta lateral de encendido y limpieza. Antes de cerrarla, al comienzo de la fusión, hay que rehacer el murete que completa el revestimiento.
Canal de colada, de plancha de hierro, revestido de masa refractaria. Mantiene la misma inclinación de la solera (10º), para hacer caer el hierro fundido en el caldero de colada.
Solera a fondo de cubilote. Consiste en arena de moldeo apisonada e inclinada 10º hacia la piquera de sangría del horno.
Plancha base de envoltura cilíndrica; de hierro colado o chapa fuerte. En su centro hay una abertura del diámetro de la solera, que puede cerrarse con un portillo de descarga de uno o dos batientes que se abren hacia abajo por medio de un cerrojo, de una palanca o quitando el puntal. A través de ella se descarga el contenido de coque de la cama, al final de la operación del horno.
Columnas de apoyo: casi siempre son cuatro, de hierro fundido y son sostenidas a su vez por unos cimientos de ladrillos de hormigón.
Crisol: es la parte inferior del cubilote comprendido entre la solera y el plano de las toberas. Se estima que el metal ocupa en él, el 46 % del volumen. El 54 % restante está ocupado por coque incandescente.
Funcionamiento del cubilote.
La reparación puede efectuarse también por medio de unos aparatos especialmente creados para este uso, que proyectan la masa refractaria contra las paredes que hay que reparar por medio de aire comprimido. Este sistema es aplicable a los hornos de dimensiones grande y mediana.
Al día siguiente se puede encender de nuevo. Algunas veces se repara durante la noche o la madrugada para fundir todos los días. Aunque esto requiere de un esfuerzo considerable por parte de los reberberistas.
Reparación. – Después de cada fusión de 3 a 10 horas, el cubilote se deja enfriar y, al día siguiente, se repara. A este fin, con un cincel o una piqueta, se quita la escoria o el material refractario vitrificado adherido al revestimiento, que se presenta más o menos corroído en torno a las toberas hasta alcanzar el material refractario que no ha sufrido deterioro. Las partes afectadas se recubren entonces con material nuevo, a mano y dejándolo reposar por lo menos 24 horas. Si el espesor a recubrir es muy grande, se utilizan trozos de ladrillos, siempre del mismo material refractario.
Dos horas antes de dar comienzo a la colada, por la portilla de encendido (o desde arriba) se introduce un montoncito de leña seca que se enciende hasta obtener un fuego abundante y vivo, favorecido por el enérgico tiro que producen la portilla de encendido, las mirillas de las toberas, la piquera de colada y la de escoria, todas abiertas, así como la propia chimenea del horno.
Se empieza entonces a introducir el coque encendido, en una capa de unos 32 cm para cada carga, a razón de 140 Kg por metro cuadrado de horno; con el coque debe mezclarse un 5 a 10 % de piedra caliza, llamada también fundente; antes de introducir una nueva capa hay que asegurarse de que el coque situado debajo esté bien encendido.
El coque de encendido debe alcanzar de 1 a 1.60 metros sobre el plano de toberas. El nivel se comprueba introduciendo por la boca de carga una cadena o una cabilla doblada en (Z), el encendido de la columna se comprueba observando el color rojo del revestimiento refractario u observando directamente los trozos de coque por la mirilla de las toberas. Se activa el encendido dando viento por espacio de 4 a 5 minutos, lo cual sirve también para desulfurar el coque.
Encendido. – Se repara la solera del horno con arena de moldear seca con una pequeña adición de grafito, arcilla y agua, secándose con fuego de leña o con una llama de fuel-oil o de gas.
La carga de coque de encendido (cama), cuya función es sostener las cargas colocadas encima y dar, con su combustión, la energía térmica necesaria, debe estar constituida por una cantidad de combustible cuya altura permanezca invariable durante toda la colada.
Para ello, el coque consumido se reintegra de modo regular a través de las cargas sucesivas de coque, que entran por la puerta de carga.
Introducción de la carga. – La carga del horno comienza colocando sobre la capa de coque de encendido una carga de coque adicionada de la necesaria cantidad de fundente y encima de esta la carga metálica. A continuación se coloca una segunda carga de coque con fundente y la segunda carga metálica, y así alternativamente hasta alcanzar la puerta de carga. A continuación, se espera un período de tiempo de 60 a 90 minutos (según el tamaño del horno), para que el coque encendido de la cama precaliente las cargas añadidas al horno. Transcurrido ese tiempo, se cierran las mirillas de las toberas y las portillas, se conecta el ventilador y si todo ha sido bien ejecutado, transcurrido de 6 a 9 minutos, se presentará el primer hierro fundido en la piquera de colada. Este hierro se considera frío y no se utiliza. Solo se emplea cuando comienza a salir caliente y con buena fluidez por el canal.
En el sistema por sifón (Pinar del Río), desde un inicio el orificio de sangría permanece abierto, el hierro y la escoria se separan en el sifón. Esto es lo que se conoce como colada continua.
Período de operación. – A partir de que el primer hierro fluye libremente por el canal de sangría, se cierra este orificio con un tapón de barro refractario. Se deben disponer de varios tapones (humedecidos, próximos al horno), ya que se utilizarán cada vez que se pique el horno. Ahora se espera a que se acumule el hierro líquido en el crisol del horno. La medida de que el crisol estará lleno le dará la salida de escoria por la piquera correspondiente. La fluidez con que salga la escoria es índice del buen funcionamiento del horno. Inmediatamente que salga toda la escoria (comienza a salir hierro, junto con la escoria), quiere decir que el crisol está lleno de hierro líquido. Entonces se rompe el tapón del orificio de sangría y se recibe el hierro en las cazuelas de vertido. Vaciado el crisol se coloca un nuevo tapón en el orificio de sangría y se repite todo el proceso. Lo descrito aquí es lo que se denomina operar el horno por picada y se hace cuando se demandan grandes cantidades de hierro de una vez o por práctica establecida.
Fin de la fusión. – Después de algunas horas de funcionamiento se comprueba la cantidad de piezas que quedan todavía por colar y se introduce la última carga, reservado para esta los trozos de metal más ligeros. Cuando el nivel de la carga alcanza aproximadamente las tres cuartas partes de la altura del horno, se reduce gradualmente el viento, cerrando por completo la entrada de aire al horno cuando está próxima la fusión del último hierro colado. Cuando aparece escoria en la piquera se vacía el horno.
Vaciado del horno. – Hay que asegurarse de que el pavimento debajo del horno esté bien seco; se abren los portillos de las toberas, se abre el canal de colada y la portilla de encendido y se hace correr cerrojo o el puntal que cierra la puerta inferior del horno. La solera del horno cae al igual que los residuos de la capa de coque y de material contenidos, que se apagan con chorros de agua y se retiran para que no se estropee el cubilote. El coque recuperado se aprovecha para las estufas o para el relleno de machos muy voluminosos. El hierro se funde para las piezas corrientes.
https://www.youtube.com/watch?v=CzImVZSUEl8
MUCHAS GRACIAS POR SU ATENCION !!!!!!!
Muy Bien el artículo...
ResponderEliminarPero cual es el que más se utiliza, en el siglo XXI..?